Après ces quelques définitions vous aurez un aperçu de l’univers du Lean management.
5S
Le 5S est un outils tiré du Toyota Production System qui consiste à organiser son poste ou sa zone de travail en suivant une méthodologie scindée en 5 étapes succesives dépendantes les unes des autres. Ces 5 étapes commencent par un s en japonais et ont pu être traduite en anglais et français de la même manière:
Seiri >
Sort >
Supprimer
Seiton >
Set in order >
Situer
Seiso >
Shine >
Scintiller
Seiketsu >
Standardize >
Standardiser
Shitsuke >
Sustain >
Suivre
Qu’est ce que le 5S apporte?
Eliminer les gaspillages, la Non Valeur Ajoutée provenant d’un poste de travail mal organisé, désordonné. Par exemple: temps perdu à chercher un outils ou temps passé à aller chercher du matériel, de la matière.
Goulot d'étranglement
Bottleneck
Un goulot d’étranglement est une étape bloquante du process qui freine la productivité provoquant des arrêts en amont comme en aval. Un des objectifs du lean management est de supprimer ces goulots d’étranglements afin de lisser la production et gagner en efficience.
Comment repérer les goulots d’ étranglement?
Une analyse précise type Value Stream Mapping (VSM) permet de cartographier un processus et ainsi connaître les points d’arrêts de celui-ci.
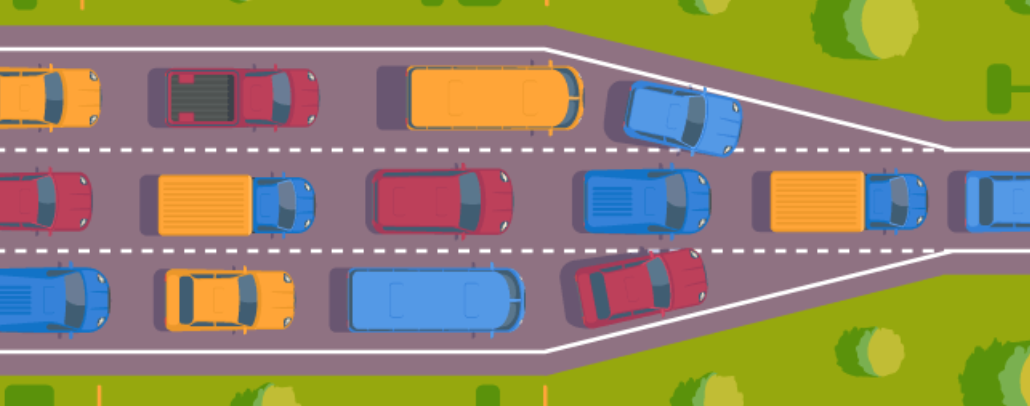
Flux continu
Continous flow
Un flux continu est une production qui vise le zéro arrêt avec un minimum ou pas de zone tampon entre les étapes du process. Pour obtenir un flux continu, on parle de lissage de production.
Comment le flux continu nous aide t-il?
Travailler à mettre en place un flux continu permet d’éliminer toutes sortes de gaspillages (muda , voir définition plus bas) : temps d’attente, transport inutile, inventaire,…)
Andon: système alerte en temps réel
Problem alert system
Système de feedback visuel qui indique l’état de la production et/ou lorsqu’une assistance est nécessaire.
Il agit comme un outils de communication en temps réel et fait en sorte de porter une attention immédiate sur les problèmes.
Gemba
Philosophie de travail qui consiste à aller voir les problèmes où ils se passent. En l’occurrence pour l’industrie cela consiste à passer du temps sur la chaîne de production avec les opérateurs et chefs d’équipes, maintenance, etc.
Qu’est ce que cela apporte?
Outre le fait de resserrer les liens opérateurs / managers , le Gemba permet de déployer des solutions objectives basées sur des faits observés et tout cela en concertation avec tous.
Juste à temps
Just in time
Le juste à temps est un ensemble de technique visant améliorer la chaine de valeur d’un processus. Sil améliore la Valeur Ajoutée, il sert également à supprimer la Non Valeur Ajoutée. Le juste à temps vise à lisser la production pour qu’elle soit en adéquation avec la demande.
« Produire ce qui est demandé par le client, ni plus, ni moins »
Kaizen (amélioration continue)
Continous improvement
Le kaizen est une philosophie de travail où les employés travaillent ensemble proactivement à la résolution de problèmes et/ou à l’implémentions d’améliorations.
Rien est jamais parfait, le kaizen est aussi une mentalité de progrès continu.
En quoi le kaizen est-il utile?
Plus qu’un simple outils, il définit la philosophie du Lean management.
Le kaizen permet de combiner toutes les compétences d’une entreprise au service de l’amélioration de la productivité.
ATTENTION: ne pas confondre KAIZEN et KAIZEN BLITZ:
Le kaizen blitz est chantier « one shot » de quelques jours où les gens se rassemblent pour résoudre un problème et améliorer un processus.
Kanban système de flux tiré
Kanban pull system
Tiré du Toyota Production System(TPS) et signifiant « étiquette » en japonais.
Le KANBAN est une méthode de régulation de flux de matière au sein de l’usine mais aussi avec le/les fournisseurs et le/les clients.
Le KANBAN est basé sur un réapprovisionnement automatique grâce à un système de carte signalant un besoin de marchandise en amont.
Quelle est l’utilité du Kanban?
Elimine le sur stockage et la surproduction. Elimine aussi l’inventaire avec un système de carte signalant quand le matériel doit être commandé.
Muda : gaspillage
Waste
Muda comprenez gaspillage en français est tout ce qui n’est pas de la valeur ajoutée dans le process de fabrication. La valeur ajoutée est ce pour quoi le client paie, un savoir faire, une transformation d’un produit par une machine, etc.
La chasse aux mudas est l’une des objectifs premiers du Lean management. Impossible de parler de Lean sans parler de Mudas.
Les mudas sont au nombre de 8. Ils peuvent se mémoriser facilement grâce au terme mnémotechnique TIM WOODS.
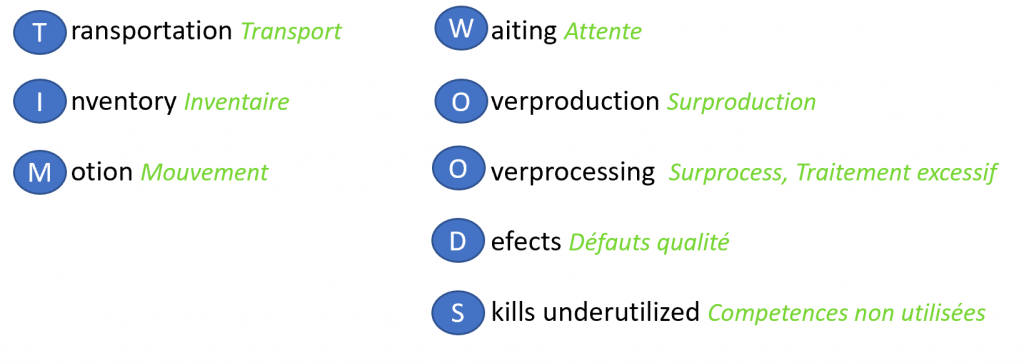
Muri : Surcharge
Overburden
Muri se définit par une surcharge ou une sur sollicitation des employés et/ou des machine. Le muri intervient lorsque l’on est au dessus de la capacité de production du système en place. Du muri découle souvent des arrêts de travail, des heures supplémentaires et un climat social tendu.Le muri est très intéressant à mesurer sur le long terme pour connaître « l’état émotionnel » d’une entreprise.
Mura : Irrégularité, disparité
Uneveness
Le mura est tout ce qui touche aux irrégularités, au manque de disparité. un opérateur n’aura pas la même manière de faire ou encore l’application d’un produit par une machine ne sera pas tout le temps identique. Toutes ces variabilités peuvent amener à une baisse de productivité.
La standardisation est le moyen pour remédier au mura.
Lorem ipsum dolor sit amet, consectetur adipiscing elit. Ut elit tellus, luctus nec ullamcorper mattis, pulvinar dapibus leo.
PoKa Yoke
Le Pola Yoke est un moyen de détection et de prévention des erreurs dans le processus de production dans le but d’atteindre le zéro défaut. Le Poka Yoke est un moyen de prévention des erreurs potentielles par la mis en place de détrompeur.
Les Poka Yoke sont souvent d’apparence trés simpliste mais évite tout doute et erreur possible.
Exemple concret de la vie de tout les jours: A la station essence, chaque pistolet est adapté au type d’essence et au réservoir, on ne peut pas insérer un pistolet essence dans un réservoir gazole et vice versa. Ou encore un détrompeur pour ne pas assembler à l’envers deux constituants comme un cable et sa prise.
Analyse causes racines
Roots cause analysis
L’analyse des causes racine est une méthodologie de résolution de problème visant comme son nom l’indique à traiter la cause première d’un problème et non ce qui en découle. Elle permet de se focaliser sur le problème source au lieu de traiter par des solutions rapides les problèmes dit « symptôme ».
« Traiter la maladie plutôt que le/les symptômes »
En quoi est ce utile?
Cela aide à garantir qu’un problème est réellement éliminé en appliquant une action corrective à la cause profonde du problème.
S.M.E.D. : Single Minute Exchange of Die
Le SMED consiste à travailler à réduire le temps de configuration(changement) entre deux fabrication différentes. En effet le temps de changement est considéré comme de la Non Valeur Ajoutée, il est donc important qu’il dure un minimum de temps.
En quoi le SMED nous aide t-il?
Le SMED permet permet la fabrication en plus petits lots, réduire les stocks et améliore la réactivité face à une demande client.
Objectifs S.M.A.R.T.
L’outils SMART s’avère très utile lorsque l’on souhaite définir un objectif. On dit que l’objectif défini doit être SMART à savoir:

Lorem ipsum dolor sit amet, consectetur adipiscing elit. Ut elit tellus, luctus nec ullamcorper mattis, pulvinar dapibus leo.
Cela permet de s’assurer de l’efficacité des objectifs définis.
Takt time
C’est le rythme, la cadence de production que l’on doit suivre pour répondre à une demande client par exemple « fabriquer une pièce toute les 50 secondes ».
Attention à ce que le takt time ne soit pas supérieur à la capacité de production d’où la nécessité du lean afin de connaître au plus juste ses moyens de production.
Standardisation
Standardization
La standardisation consiste à écrire des procédures documentées pour la fabrication qui capitalisent les bonnes pratiques.
Il s’agit d’une documentation vivante facile à modifier.
Un standard n’est pas une procédure gravée dans le dur , bien au contraire il permet de figer une manière de faire à un instant t pour une période jusqu’à une mise à jour suite à amélioration.
Maintenance productive totale
Total productive maintenance
TPM
La TPM vise à maximiser le temps de fonctionnement des équipement en s’appuyant sur la maintenance préventive et proactive. La TPM mêle la maintenance avec la production où on implique les opérateurs dans l’entretien de leur machine.
« Crée une responsabilité partagée des équipements entre maintenance et production »
Cartographie de la chaîne de valeur
Value Stream Mapping
V.S.M.
La Value Stream Mapping est selon moi l’outils le plus pertinent pour toute analyse de l’existant.
Il permet de cartographier les flux de matières et d’informations et fait facilement ressortir les opportunités d’amélioration.
C’est un travail de terrain qui s’effectue sur le mode GEMBA. On commence du client en remontant jusqu’au fournisseur à la manière d’une enquête où l’on remonte sur les traces du produit.
Souvent réalisé pour transformer la production en flux tendu.
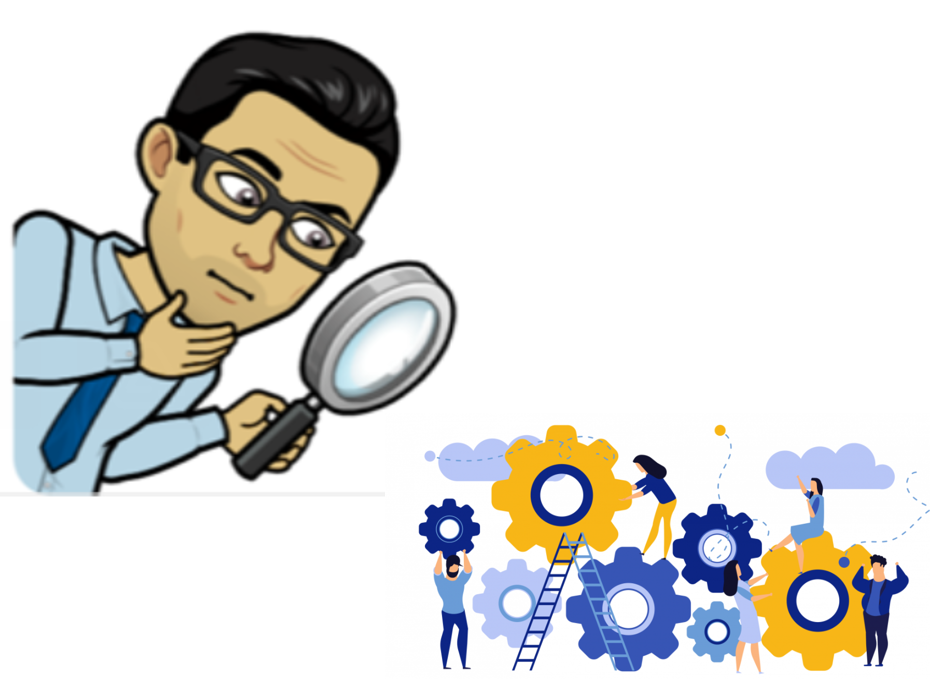
Management visuel
Visual management
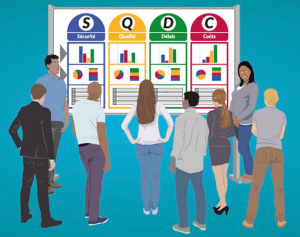
Le management consiste à mettre en avant les indicateurs pertinents pour la production.
Le management visuel a de nombreux avantages:
1 Avoir accès rapidement aux informations clefs
2 Favoriser le partage d’idée
3 Favoriser la communication interne
4 Instaurer un feed back régulier
5 Favoriser le pilotage de plan d’actions
Le management visuel s’articule très souvent autour de 4 grands axes Sécurité Qualité Cout Délai
Jidoka : Autonomation
Automation
Concevoir une ligne de production pour s’arrêter automatiquement lorsqu’un défaut est détecté.
Heijunkan : lissage de production
Level scheduling
Méthode d’ordonnancement qui consiste à produire en lots plus petits et plus variés.
Hoshin kanri
Policy deployment
Aligner les objectifs stratégiques d’une entreprise avec le travail effectué en production.
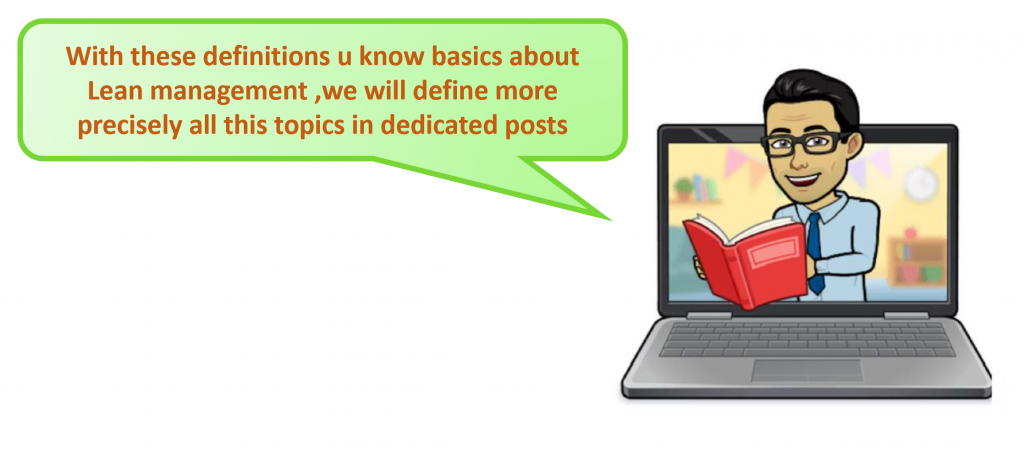
Thank you
Quelque chose s’est mal passé.
The form collects name and email so that we can add you to our newsletter list for project updates. Checkout our privacy policy for the full story on how we protect and manage your submitted data!
Soyez le premier à commenter